In the world of 3D printing, mastering 3d printing problem-solving is essential for both beginners and seasoned professionals. This technology, while revolutionary, can present a variety of challenges. Understanding these common issues and their solutions can significantly enhance your printing experience.
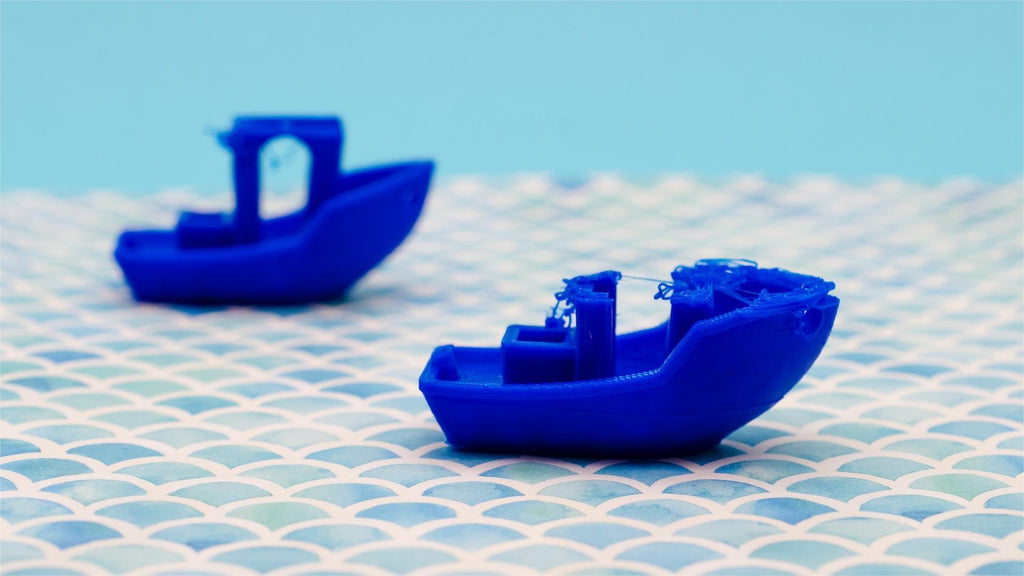
1. Warping
Warping occurs when the edges of a print lift from the build plate, leading to a distorted final product. This issue is often caused by temperature fluctuations or improper adhesion. To combat warping, consider the following:
- Use a heated bed to maintain consistent temperatures.
- Apply adhesives like glue sticks or hairspray to improve bed adhesion.
- Ensure that your print settings are optimized for the material you are using.
2. Stringing
Stringing refers to the fine strands of plastic that can appear between parts of a print. This issue can be frustrating, but it is often a result of incorrect retraction settings. To minimize stringing, you can:
- Adjust the retraction distance and speed in your slicer settings.
- Increase the temperature slightly to improve flow.
- Enable features like "Combing" in your slicer software.
3. Layer Separation
Layer separation occurs when the layers of a print do not adhere properly to one another, leading to structural weaknesses. This can be caused by insufficient temperature or speed settings. To address this issue, consider:
- Increasing the nozzle temperature to improve layer adhesion.
- Reducing print speed to allow for better bonding.
- Using a different filament that may adhere better.
4. Under-extrusion
Under-extrusion happens when the printer fails to deliver enough filament, resulting in gaps and weak spots in the print. This can stem from various factors, including clogged nozzles or incorrect settings. To fix under-extrusion, you might:
- Check for clogs in the nozzle and clean it if necessary.
- Ensure that the filament is feeding correctly and not tangled.
- Adjust the flow rate settings in your slicer software.
5. Over-extrusion
Over-extrusion is the opposite of under-extrusion, where too much filament is deposited, leading to blobs and uneven surfaces. This can be resolved by:
- Calibrating your extruder steps per millimeter.
- Reducing the flow rate in your slicer settings.
- Using a smaller nozzle size for finer details.
Conclusion
Mastering 3D printing problem-solving requires a keen understanding of these common issues and their solutions. By addressing warping, stringing, layer separation, under-extrusion, and over-extrusion, you can significantly improve your 3D printing outcomes. For a more comprehensive guide, visit this troubleshooting guide.